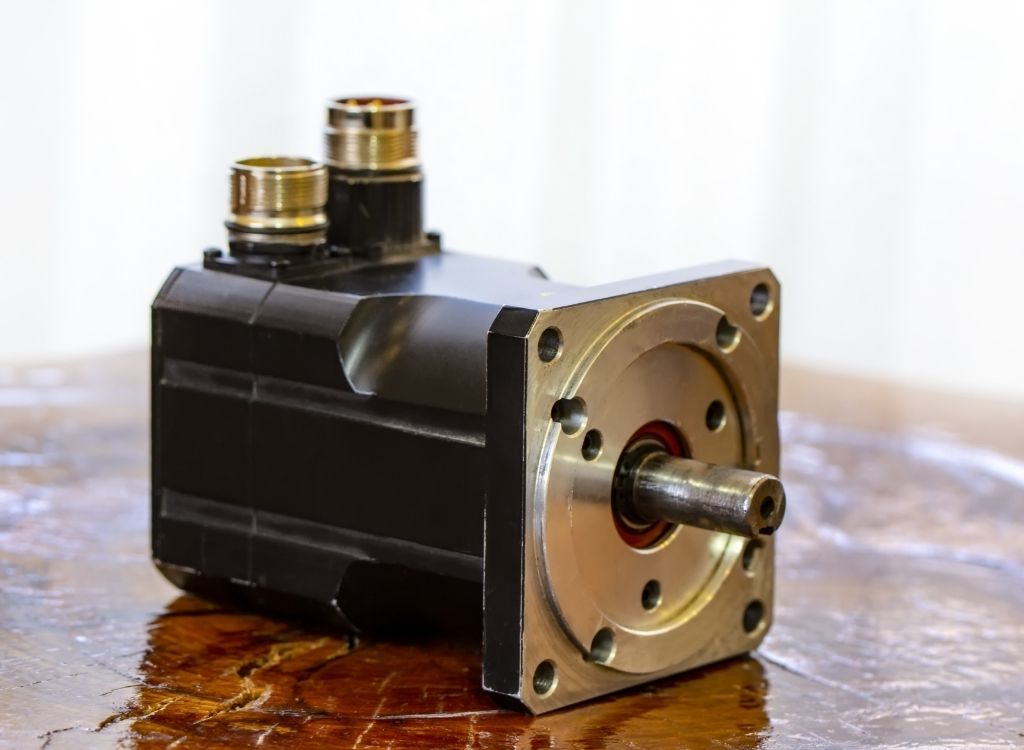
Direct current motors find use in motion control, CNC, and other automation applications that call for high speeds matched with high precision. Two types of DC motors stand out for powering this machinery: stepper motors and servo motors. While stepper motors are inexpensive and useful pieces of technology, the advantages of servo motors over stepper motors make the stepper’s “big brother” the motor of choice in applications where performance matters. Let’s take a closer look at what distinguishes the servo motor from its simpler counterpart.
Table of Contents
Torque
Nothing sets servos and steppers further apart than the advantage in torque that a servo motor provides. Torque is the application of rotational force to an object. Think of a screwdriver—you could try to turn a screw by hand, but using a tool to fit into the head of the screw gives you more torque. Both steppers and servos can produce high torque at low speeds. However, stepper motors, being far simpler mechanisms, lose torque as speed increases—sometimes quite rapidly. Servo motors, through the inclusion of gears, maintain high torque while operating at high speeds. This addition in force makes it possible for CNC tools using servo motors to work with harder materials, such as metals or particularly durable plastics, without the resistance of the material overwhelming the cutting tool.
More Sophisticated Control
While simple voltage tells stepper motors what to do, servo motors report to external controllers that give more detailed instructions than what a stepper can work with. Communication between a motor and controller is a dialogue—the motor gives a positioning signal to the control to let it know where it’s starting from. The increased complexity of servo motors means that you’ll see signs of it needing repair more often than you will with stepper motors, which typically work until they fail altogether. Nonetheless, this is a worthwhile trade-off for increased performance.
High RPM
One of the key advantages of servo motors over stepper motors is that a servo motor can maintain torque at higher speeds than a stepper motor—and it can achieve higher speeds in the first place. A stepper motor can generate up to around 1,200 revolutions per minute. This is impressive, but insufficient in high-performance industrial situations. Meanwhile, a servo motor can leave a stepper in the dust with well over 3,000 RPM. When taking the force management of the gearbox into account, this makes the servo motor the clear choice.